Optical interconnects have been around for a couple of decades, but have been primarily limited to data centers and telecom applications to meet the needs of high-bandwidth and long distances that were just not feasible with copper. Now, optical interconnects are expanding to applications not even dreamed possible or feasible just 20 years ago, driven by the ever-increasing need for bandwidth in applications that extend far beyond controlled data center environments. Let’s explore some of these new frontiers to better understand when, where and why optical interconnects are starting to be deployed.
The Copper Cliff
Many of the new and expanding applications of optical interconnects are coming about because of the ever-increasing need for bandwidth, particularly for video. Gone are the days when simple copper cables could support all of the necessary bandwidth. Video data rates for 1080p were just 9 Gbps, whereas 4K requires 18 Gbps, 8K needs 48 Gbps, and future needs are expected to easily reach beyond 100 Gbps. And these higher-resolution displays and cameras are finding their way into cockpits, cars, and consumer electronics. Plus, optical interconnects have some additional benefits over copper cables: immunity from electromagnetic interference (EMI), lighter weight, and more flexible routing options. To understand why optical interconnects are only now beginning to be widely deployed in so many new applications, we need to look at the components that make up an optical interconnect.
What is an Optical Interconnect?
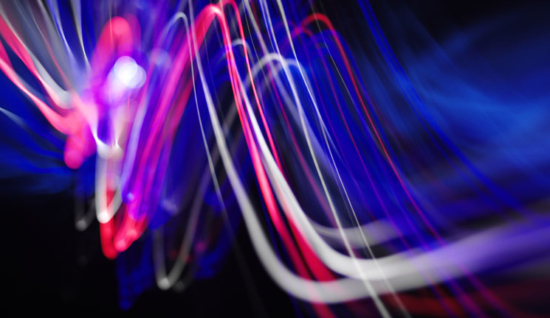
What exactly is an optical interconnect and how is it different from a good, old-fashioned copper cable? A copper cable sends an electrical signal from point-A to point-B. An optical interconnect does the same thing, but instead of sending that signal using electrons, the signal is converted to light and transmitted along an optical fiber, where it is then converted back to an electrical signal at the other end. Fiber cables have come a long way in their uniformity and ruggedness in the past 30 years, to the point where there are cables and connectors that can be installed in almost any environment. VCSELs have also improved their reliability and performance drastically over the past 20 years, to where they can operate well beyond a controlled data center environment, supporting -55C to +125C wide-temperature applications.
Applications of Optical Interconnects
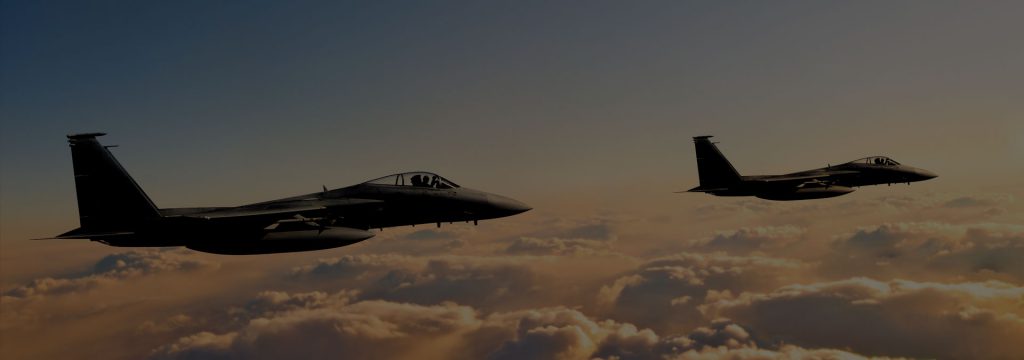
Aircraft applications of optical interconnects are really starting to take off, driven by both digital flight decks and in-flight entertainment systems. When the flight systems include 4K cockpit displays, sensor systems, and radars, there needs to be a high-bandwidth interconnect. And as commercial aircraft look to provide more in-flight entertainment run directly to seat displays, the bandwidth needs just continue to increase. When it comes to aircraft, optical interconnects are especially attractive due to the weight savings and smaller size. A current widebody passenger jet has about 500 km of wires weighing about 7400 kg, or 3% of the total aircraft weight, so there is a definite opportunity to reduce the weight, which directly correlates to improved performance and reduced fuel cost. Fiber cables have a legacy reputation as being extremely fragile, so there has been reluctance to move to fiber in a flight environment, but much progress has been made by fiber manufacturers, so much so that fiber is now flying on fighter jets and satellites. And the trend is expected to continue, as both fiber networks and point-to-point optical interconnects become the common design platform, as is reflected in the industry’s continued work on standards addressing these areas through the Airlines Electronic Engineering Committee Fiber Optics Subcommittee working to address both fiber and optoelectronic devices through updates to ARINC 803 and ARINC 804.
The development of electric aircraft is another new frontier for optical interconnects. All electric aircraft will need to be very conscientious of weight in their designs. This is particularly true for those looking to support the regional markets where both passenger numbers and range are important because the energy density of lithium-ion batteries is currently about 0.7MJ/kg whereas jet fuel is 45MJ/kg, so it packs a lot more power. All-electric aircraft also have the additional challenge in that using electric power, they do not burn fuel and thus reduce weight, throughout the flight. Plus, there will be some very high voltage electric cables, with 500V systems currently being designed and even higher voltages being considered, that can cause some serious noise issues for copper cables, which would then require more shielding leading to more weight. Optical interconnects, being immune to EMI and lightweight, would alleviate many of the routing challenges while still providing extremely high bandwidth interconnects.
Automotive is another new frontier for optical interconnects. While low-speed point-to-point interconnects over large-core fiber have been deployed for years, the automotive industry is now looking to implement high-speed in-vehicle networks to support the vast amount of data required for all of the cameras, radar, lidar, and other sensors needed for automated driving systems.
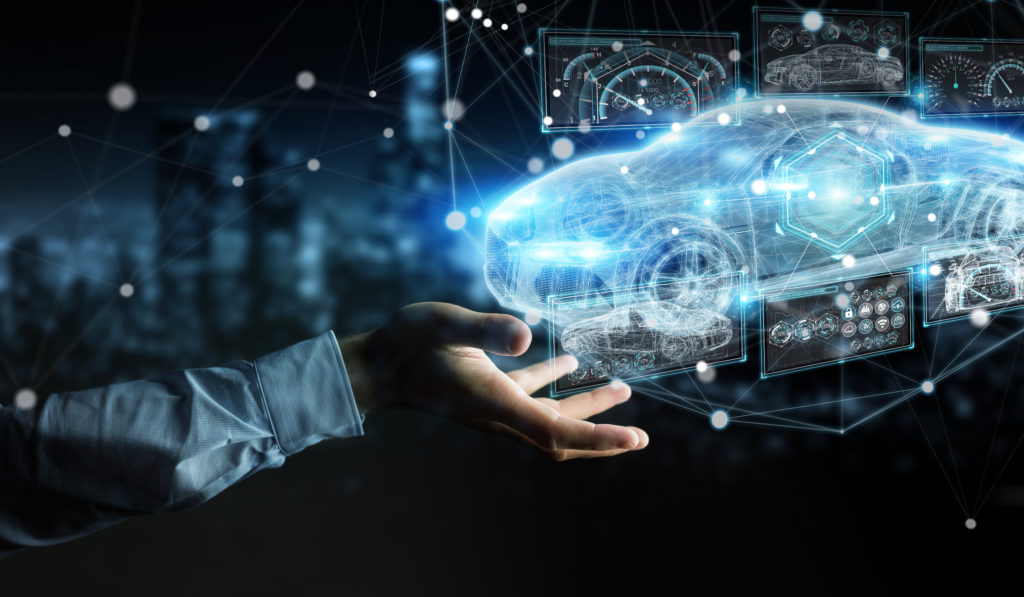
The cable harness is typically a very complex assembly that is about 30% of the total weight of the car and 50% of the labor cost, since each one is built separately. So, moving to a network architecture has some definite advantages! It should simplify the cable harness and reduce both the component and labor costs. An optical in-vehicle network has even more advantages in that it will be much lighter (key for electric vehicles) and is immune to EMI, which is important in the noisy electrical environment of an automobile. Work on developing an Ethernet standard specifically for this environment is currently underway in the IEEE802.3cz Multi-Gigabit Optical Automotive Ethernet Task Force.
Fiber is finding its way into the homes of average consumers as well, opening up a whole new range of optical interconnects in consumer electronics. Video is driving this demand, as 4K becomes commonplace and 8K is beginning the adoption curve.
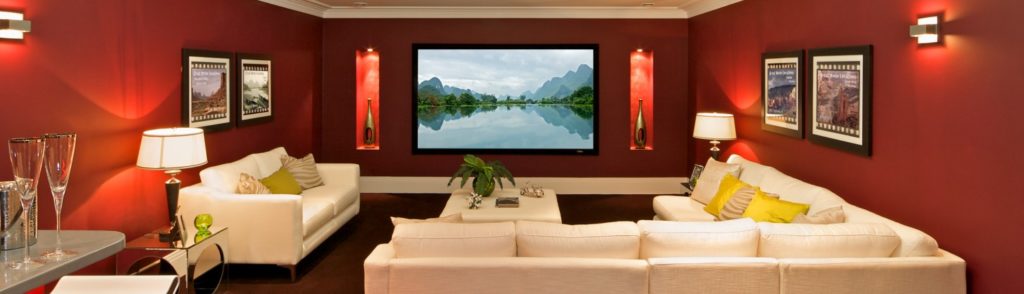
Where a simple passive copper cable could support uncompressed video up to 25 ft for 4K video for HDMI 2.0, that drops to just 16 ft for uncompressed, full-bandwidth 8K video for HDMI 2.1, which is just too short for many installations. This is opening up many new opportunities for optical interconnects in the consumer electronics market to support the higher video bandwidths, and the consumer’s appetite for video quality is just going to keep increasing, continuing to drive the need for optical interconnects.
Taking Connectivity to the Next Level
Bandwidth needs have opened new frontiers for optical interconnects in the videocom, automotive, industrial, aerospace, and defense markets. Inneos has over 20 years of experience in optical interconnect design and manufacturing, so we can help you easily and confidently integrate optical subsystems to take your connectivity to the next level.